The session began with pieces of loose fibers, and ended with beautiful yarn that can be woven into linen fabric. The Spinning Workshop with expert Andrea Myklebust, sheperd and weaver, led a select and enthusiastic group of New School students through the process of what it’s like to turn flax into linen, from stalk to finished cloth.
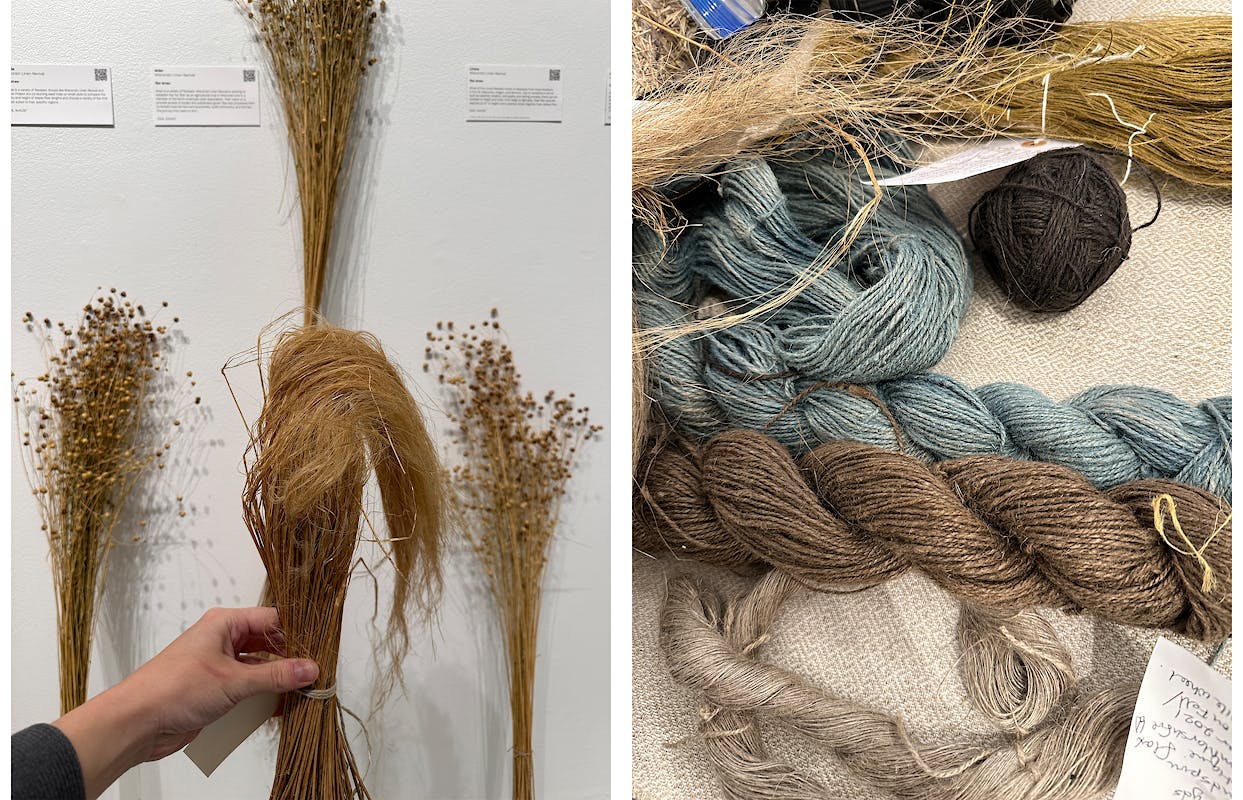
left: flax fiber, right: linen yarn
Andrea presented about her work growing and processing flax for fiber in Vermont at Mountain Heart VT. Andrea is an educator who conducts research on flax retting methods and fiber hemp. She has been growing and processing flax for fiber since 2012. She believes “a revitalized bioregional textile infrastructure centered in cloth made from flax, hemp and wool, will help meet the existential challenges of climate change.”
Andrea Myklebust presents her research prior to the spinning workshop
Spinning is the process of adding twist to a fiber, which provides strength. Yarn can be spun in two directions: when spun counterclockwise, it has a S-twist, or when spun clockwise to the right, it has a Z-twist. When only spun once, they are referred to as singles. When multiple yarns are spun together, they are plied. The number of yarns spun together refers to the number of plys, such as 2-ply, 3-ply, or 6-ply yarns.
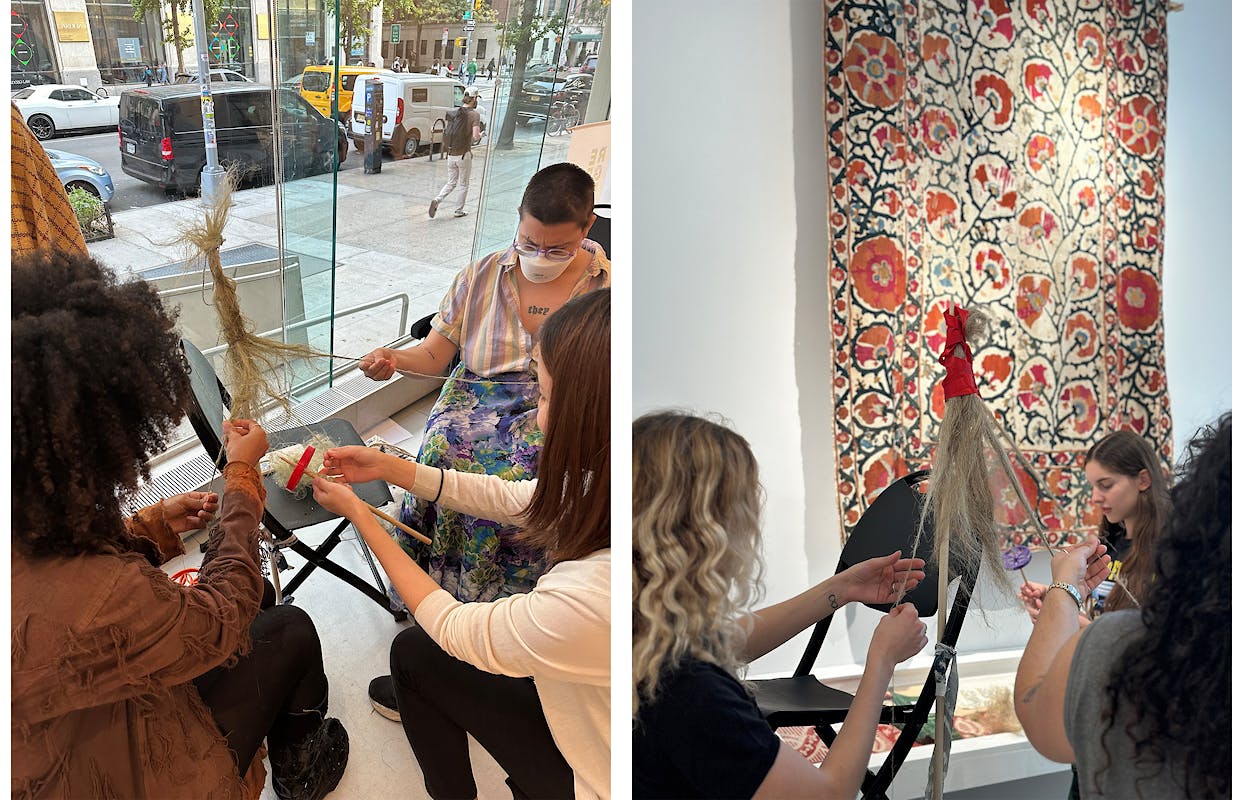
students drafting fiber from a distaff during the workshop
Flax has both long and short fibers; both can be spun into yarn. The long fibers are referred to as line. This is where the term linen originates, as well as other familiar terms such as lingerie (linen was often worn next to the body due to its breathability and moisture wicking ability) and lint (the processing of flax produces dust). The short fibers are often called tow and produce a coarser yarn. Myklebust demonstrated how to use a distaff, a long stick used to organize and hold the fibers prior to being spun. The loose fibers are drafted, or individually pulled to form a uniform fiber for spinning.
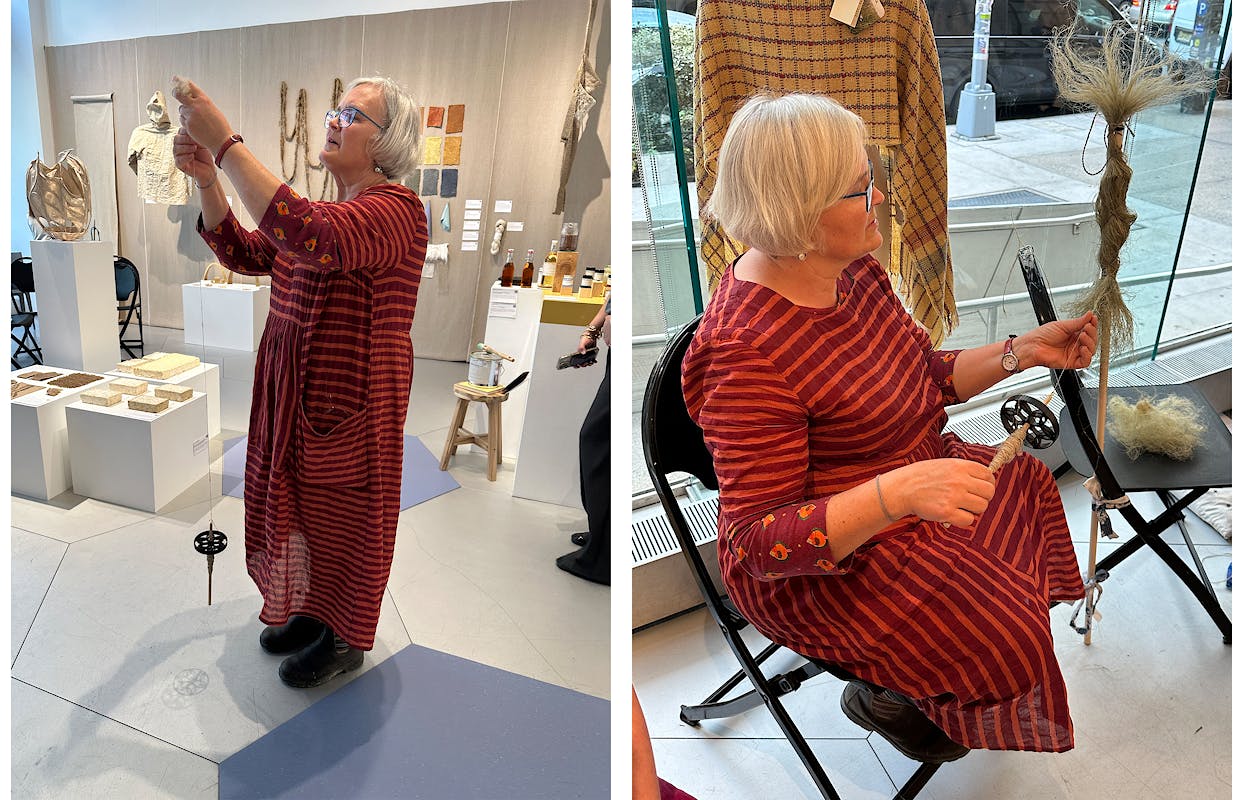
Myklebust demonstrates spinning flax fibers
Linen is typically wet spun (including water in the spinning process) to ensure fiber consistency and smoothness. Myklebust demonstrated how to spin flax on both a drop spindle and a low whorl spindle. A spindle is a simple tool of a shaft and a whorl, a weight added to fit onto the shaft to control rotation. In the examples below, the whorl is a bead or 3D printed piece added to a dowel. With a low whorl spindle, the whorl is at the bottom of the shaft and provides more control over the spun fiber. A drop spindle allows the spinner to release their hands from the spinning action and focus on drafting fiber.
left: linen yarn spun on low whorl spindle, right: linen spun on drop spindle
Andrea wrapped up the session by showing how cordage is made, which is the earliest form of plying fiber. It was inspiring to participate in the process of turning a plant into a useful yarn product, which could then be woven into cloth. The students learned new skills and were able to take home their spun yarn, with many excited to work with flax fiber in their future projects.
“It was an incredible opportunity and experience. I will definitely be using the flax and tools in future projects!” -Andre Delgado, workshop participant
The Regeneration of Flax Exhibition closes November 12th. We hope you can make it before it closes! Located at the Arnold and Sheila Aronson Galleries, 66 Fifth Avenue at 13th Street, New York, 12-6pm daily.
Read More
Join Our Academic Network
Get Access to our carefully researched and curated academic resources, including model syllabi and webinars. An email from an academic institution or a .edu email address is required. If your academic institution does not use .edu email addresses but you would like to join the network, please contact healthymaterialslab@newschool.edu.
Already have an account? Log in