Spring 2020 HempLime Workshop_Parsons Healthy Materials Lab
Parsons Healthy Materials Lab HempLime Workshop
Tucked away in a warehouse in Sunset Park, Brooklyn’s sprawling Industry City complex, next to fashion start-ups and microbreweries, Parsons Healthy Materials Lab (HML) has an “invention in progress.” Perhaps it would be better titled a “reinvention in progress.”
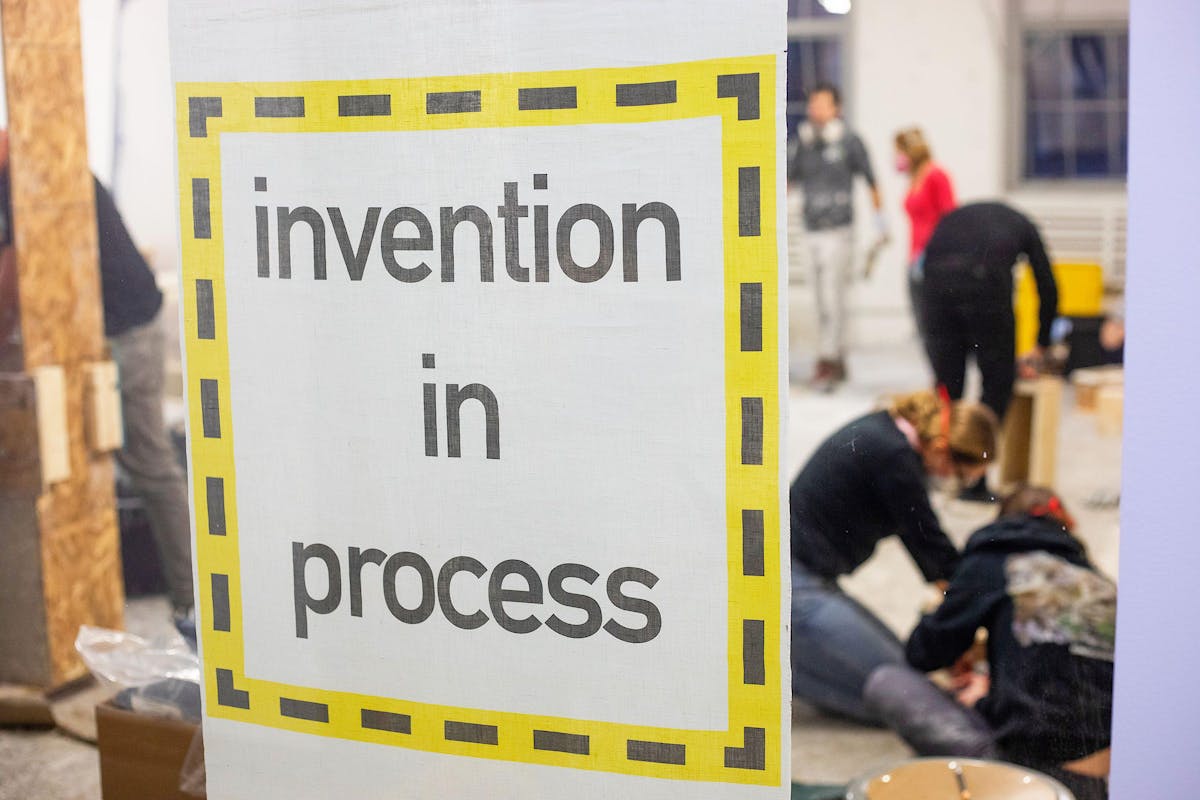
Along with our collaborators from COEXIST, we at Healthy Materials Lab are workshopping a material we believe can overhaul the building industry. While hemp and lime have been used in construction for centuries, legal barriers have wiped this practice from the American memory. HML and Coexist are reviving the tools, infrastructure, and industry needed for a HempLime revolution. That’s a big goal and we thought it would be best to start small. So, at the end of January 2020 students from Parsons Master of Architecture program, BFA Architectural Design, MFA Interior Design, and MFA Industrial Design gathered to get their hands dirty and learn the basics of making HempLime building products.
Building with HempLime is refreshingly simple.
Building with HempLime is refreshingly simple. Before the students arrived we brought in everything needed to create this building material from scratch. Bales of hemp hurd were piled in one corner and 50 lb bags of lime were stacked on the opposite side of the room. The only other thing needed to begin the mixing process were some large buckets of water.
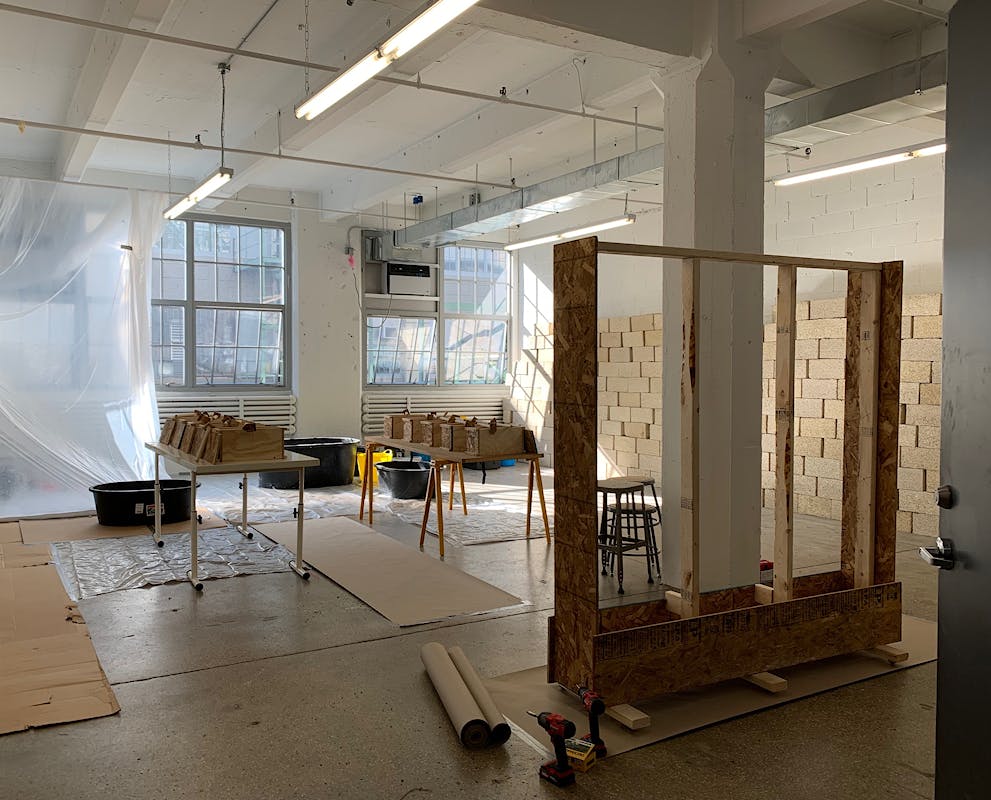
But the ingredients to make HempLime weren’t the only things in the room. Lining one wall of the space was a collection of completed HempLime Blocks. These were stacked against a painted cinderblock wall. The contrast between the old painted concrete block warehouse wall and the wall of HempLime blocks in front of it was clear. The concrete blocks were cold and uninviting and the hemp and lime practically magnetic. As the students arrived they all flocked to the hemp wall to touch the blocks. Without fail, the students smelled the blocks. They placed their ears close to the blocks and listened.
Healthy Materials Lab Design Director Jonsara Ruth pried the students away from the hemp blocks and gathered them around the wooden molds that would, in just an hour’s time, produce new HempLime blocks. Ruth introduced Anastasiya Konopitskaya and Drew Oberholtzer who, together, as COEXIST Build, are growing hemp and developing hemp-based building materials on their farm in Eastern Pennsylvania. Konopitskaya and Oberholtzer presented a brief introduction to the wonders of building with hemp, and could not help but rattle off praises of the plant. They explained the process of constructing HempLime blocks and students eagerly broke up into groups to tackle each stage of the work.
In the back corner of the large workshop space, tarps were hung from the ceiling to contain the dust from the lime mixing station. Students wore goggles, respirators, and ear protection as they mixed lime with water, which was by far the messiest stage of the process. Next, students poured the lime mixture into large buckets filled with dry hemp hurd. This stage of the process was more like cooking than construction. Students scraped the bottom of the buckets to ensure a thorough mixture. Oberholtzer instructed them to make a ball out of the hemp and lime mix. To test the mix, students poked their finger into it and if it crumbled into three different pieces, they had the mixture right. Like good cooking, this part of the process relied on both intuition and experience.
Over the day-long workshop, two groups of students worked with hemp and lime. Students transported the HempLime mixture to the molds and compacted it to form sturdy blocks. They were instructed to tamp down the hemp and lime… but not too hard. Applying more pressure to the edges ensured stability while leaving the center of the block looser to allow for air circulation. It is a delicate balance to make a HempLime block which acts as a naturally fire-resistant insulator and a vapor-permeable surface for a wall.
This day-long experience fueled the design process for the spring semester as students returned to their desks to tackle the challenges of this semester—to design affordable housing using HempLime building products
At the end of a long day, over 50+ Parsons students and faculty (David Lewis, Emily Moss, Alison Mears, Mark Gardner, Marcus Carter, Eirini Tsachrelia, and Jonsara Ruth) with COEXIST had created almost 100 new HempLime blocks and half of a freestanding 12” thick wall. Students, experts, and faculty alike had messy work clothes. While the students’ work gloves were specially coated, they had gained tactile knowledge about a new-found building material made essentially from a plant and a rock. This day-long experience fueled the design process for the spring semester as students returned to their desks to tackle the challenges of this semester—to design affordable housing using HempLime building products as the primary construction material, to reimagine new buildings on the Lower East Side of Manhattan and propose new ways of designing and making interior spaces.
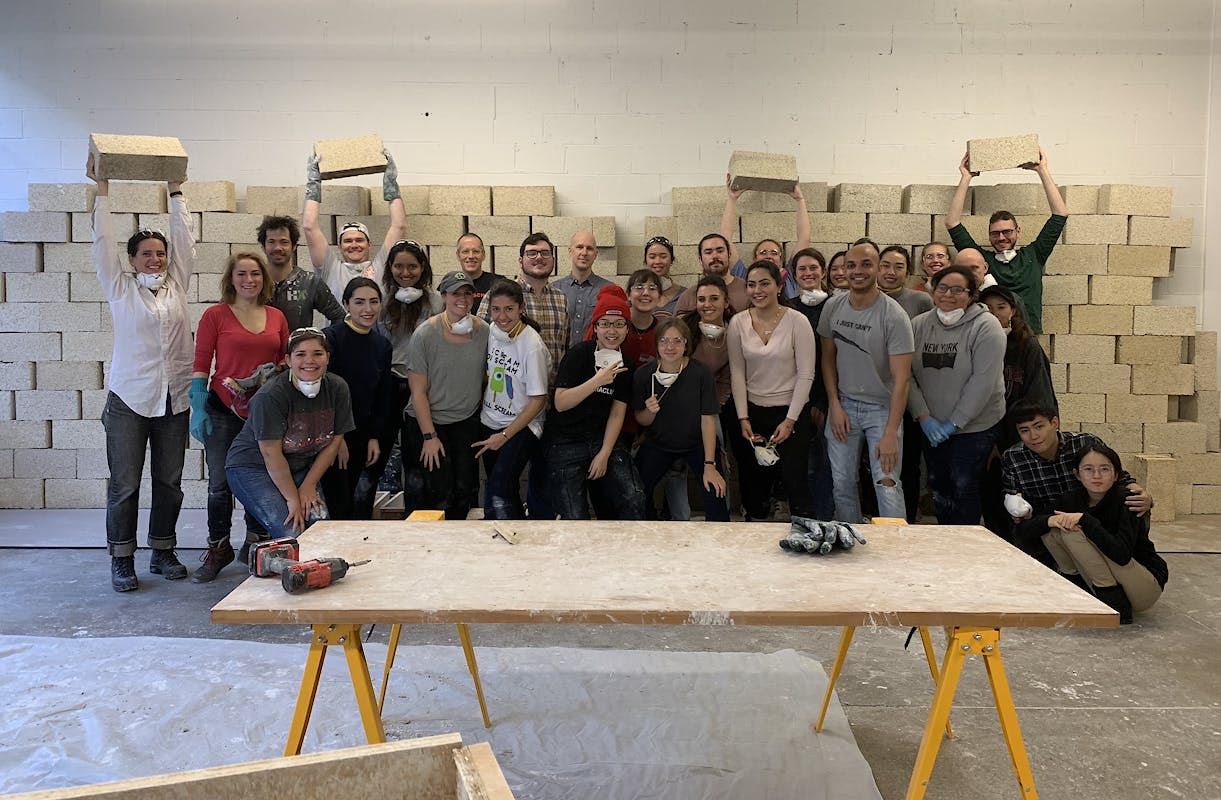
The plan for the Spring 2020 semester was to build two full-scale installations in the space in Industry City: one pavilion would be constructed from HempLime so that visitors would understand the full sensorial qualities of the material.. The other installation would be made of conventional building materials. Visitors would be able to evaluate for themselves why building materials made from HempLimewill present new opportunities for architects and designers. These plans are on hold until we can all be together in one space.
Meanwhile, we will keep researching all of the positive aspects of this new construction practice that could revolutionize future residential construction in the US.
Read More
Join Our Academic Network
Get Access to our carefully researched and curated academic resources, including model syllabi and webinars. An email from an academic institution or a .edu email address is required. If your academic institution does not use .edu email addresses but you would like to join the network, please contact healthymaterialslab@newschool.edu.
Already have an account? Log in