BLOG
October 17, 2016
Role Models: Healthier Modeling Material Alternatives - Investigations by Del Hardin Hoyle
Darcy Bender
This semester, Parsons opened the doors to its new making center which will serve as a space for students to explore new techniques and tools for making and prototyping. Unfortunately, the materials used in the lab are not always so innovative. Many materials used by students in the fabrication shops on campus contain chemicals that are known to be harmful to human health. The building insulation material, extruded polystyrene (XPS) foam, is often used by Parsons students to make models and to prototype product designs. XPS is made from a petroleum-based plastic that is not only a non-renewable resource, it also contains added flame retardants that can be harmful if ingested or inhaled.[1] Our partner, the Green Science Policy Institute has done extensive research into the utility of the flame retardants in foam insulation and their effect on humans and the environment. They have found that XPS foam has been linked to reproductive and developmental harm in humans. Because design students are experimenting with the material and cutting it with tools that create dust and smoke, they could have a higher risk of being affected by the material than a professional installer of insulation.
The Healthy Materials Lab began looking for alternatives to XPS foam with student safety and wellness as the primary focus, but we were quickly inspired by how these new products have the potential to transform how our students and faculty think about materials in the design process.
One material that really stood out was ecovative’s Myco Foam, a packaging product made from agricultural waste and mycelium mushrooms. The white foam can be grown in molds of any shape and has a smooth, soft exterior. It can be purchased as a finished product, but the company also sells “Grow It Yourself” kits to experiment with the growing process.
Green Cell Foam, a corrugated foam made from GMO-free cornstarch, can be dissolved in water or composted at the end of its life.
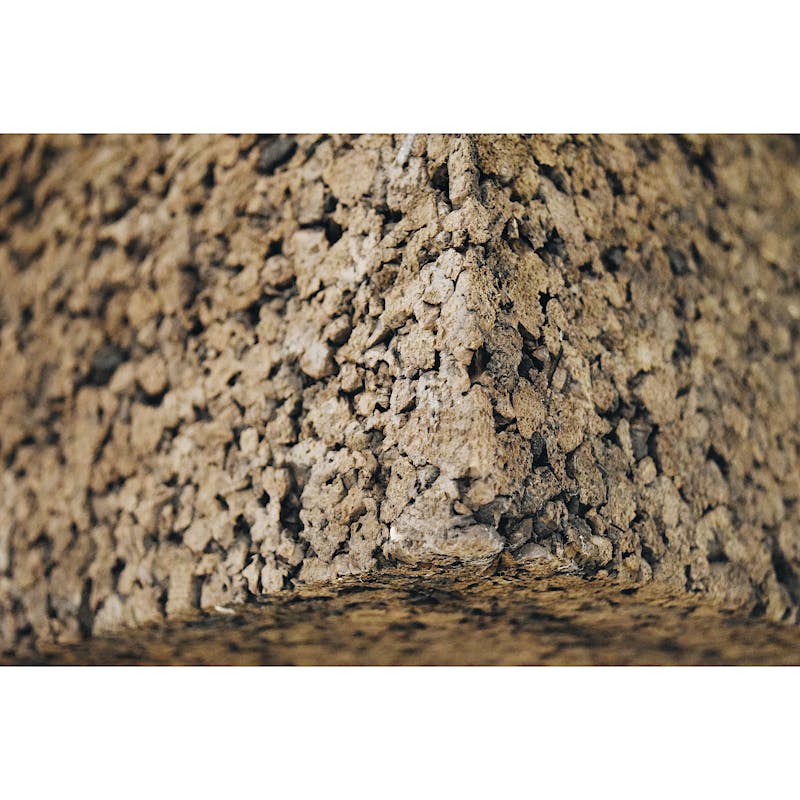
The expanded corkboard by the Portuguese company Amorim Isolamentos has a dark wood color and a grainy texture. It is manufactured using a process that requires no additives so that the final product is made entirely of cork. While none of these products have the exact qualities of XPS foam, they certainly can be used by students interested in exploring new textures, densities, and manipulation processes.
In order to test the functionality of these materials in the fabrication process, we asked Del Hardin Hoyle to experiment with them. We’ve created an exhibit of the results of his testing which is on display at the Donghia Materials Library for the Fall 2016 semester. We hope our research inspires students to think about their material choices in a new way and can’t wait to see how they use these materials to make (or grow) their innovative designs.
[1] Vytenis Babrauskas , Donald Lucas , David Eisenberg , Veena Singla , Michel Dedeo & Arlene Blum (2012) Flame retardants in building insulation: a case for re-evaluating building codes, Building Research & Information, 40:6, 738-755 http://greensciencepolicy.org/…
Read More
Join Our Academic Network
Get Access to our carefully researched and curated academic resources, including model syllabi and webinars. An email from an academic institution or a .edu email address is required. If your academic institution does not use .edu email addresses but you would like to join the network, please contact healthymaterialslab@newschool.edu.
Already have an account? Log in